Due to the extreme temperature difference between liquid nitrogen and ambient air, a large amount of heat will transfer even through a very short section of uninsulated or poorly-insulated pipe component very quickly. This can have a substantial impact on the entire system.
Even though the loss is not immediately visible nor is it significant for one day, but over time that loss can add up to thousands of dollars. Increased heat leak at any point in the system can cause two-phase fluid that increases pressure drop, causing irregular flow of liquid, which reduces the overall flow rate. Two- phase flow will create significantly higher pressure drops through the pipe system, irregular liquid delivery, results in warmer liquid at the cryogen use point and shortens the life of valve seats and other components within the system.
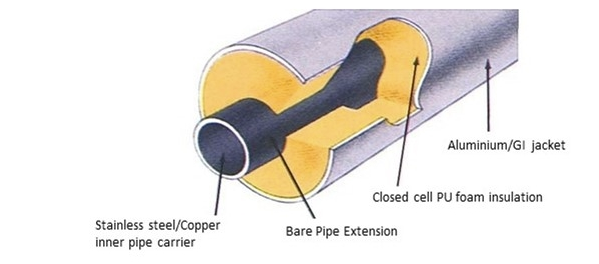
Consider a food production company that utilizes a 30-meter (100-foot) run of vacuum jacketed pipe (VJP), along with a 0.5-meter (2-foot) connection of foam-insulated pipe.
For the VJP with a diameter of 1.0 inch, the typical heat transfer rate is approximately 0.5W/m (0.52 BTU/hr/ft). Thus, the total heat leak for the 30-meter run of VJP can be calculated as 30 x 0.5 = 15W (52 BTU/hr).
On the other hand, for the foam-insulated copper pipe, the typical heat transfer rate is around 20W/m (20 BTU/hr/ft). Consequently, the heat leak for the 2-foot section of foam-insulated copper pipe can be determined as 0.5 x 20 = 10W (40 BTU/hr).
Result:
The 0.5m(2-foot) section of foam insulated copper pipe is responsible for 40% of the total heat transferred into the pipe.
Total heat leak for the 30m run of fully vacuum insulated pipe is 15W.
The heat leak for the 30m VJP system plus the 0.5m foam insulated copper pipe is 25W, which translated to 0.56L per hour of liquid nitrogen loss.
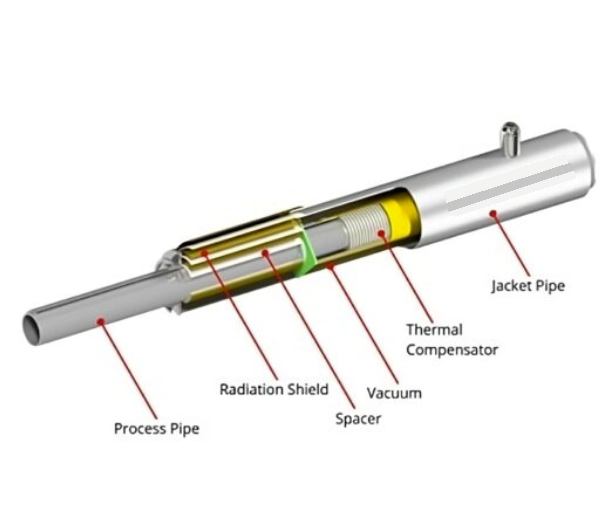